Manganese, an essential metal with various industrial applications, exists in several oxidation states, two of which are particularly important for industrial processes: manganese dioxide (MnO₂) and manganese oxide (MnO). These two compounds play vital roles in industries ranging from metallurgy to battery manufacturing. This blog delves into the chemical relationship between manganese dioxide and manganese oxide, the reduction process involving carbon, and the significance of controlling the reduction temperature.
Keytakeaways: manganese dioxide to mangaese oxide reduction temperature using carbon
Manganese dioxide (MnO₂) and manganese oxide (MnO) are both oxides of manganese, but they differ significantly in terms of their chemical structure and properties.
-
Manganese Dioxide (MnO₂): Manganese dioxide is a black or brown solid and one of the most stable forms of manganese. It is typically found in nature as the mineral pyrolusite. In its structure, manganese exists in the +4 oxidation state. MnO₂ is often used as a precursor in the production of various manganese-based compounds and has key applications in the production of dry cell batteries, particularly in alkaline and zinc-carbon batteries.
-
Manganese Oxide (MnO): Manganese oxide, on the other hand, is a compound where manganese is in the +2 oxidation state. MnO is typically produced through chemical reduction processes, such as when manganese dioxide is reduced in the presence of a reducing agent like carbon. Manganese oxide is highly valued in various industrial processes, including the production of steel, where it acts as a deoxidizing agent, and as a catalyst in some chemical reactions.
The chemical reaction involved in the reduction of manganese dioxide to manganese oxide is a key step in the processing of manganese ores, particularly when aiming to produce higher-purity manganese for industrial use.
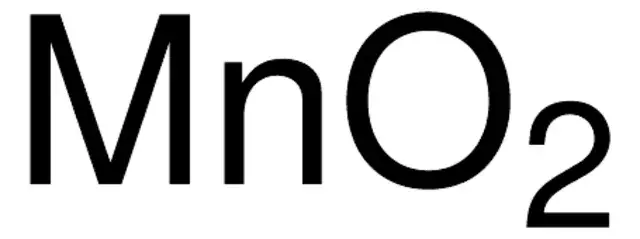
2. Chemical Relationship Between MnO₂ and MnO
The relationship between manganese dioxide and manganese oxide can be understood through a simple redox reaction. In this reaction, manganese dioxide (MnO₂) is reduced to manganese oxide (MnO) by a reducing agent, typically carbon (C). The reaction can be represented as follows:
In this reaction, carbon donates electrons to reduce manganese from the +4 oxidation state (in MnO₂) to the +2 oxidation state (in MnO). The carbon is oxidized, releasing carbon dioxide (CO₂) as a byproduct. This type of reduction reaction is commonly used in the metallurgical industry to produce manganese oxide from manganese ores.
3. Reduction Process of MnO₂ to MnO Using Carbon
The reduction of manganese dioxide to manganese oxide using carbon is a crucial process in the extraction and purification of manganese from its ores. This reaction typically occurs at high temperatures, where carbon acts as the reducing agent, helping to remove oxygen from the manganese dioxide.
The process is conducted in furnaces or reactors where temperatures can reach over 700°C. As the temperature increases, the rate of reduction accelerates. The carbon reduces MnO₂ to MnO, releasing CO₂ in the process.
Reduction Temperature: Importance and Influence
One of the most critical factors in this reduction process is temperature. The temperature at which this reaction occurs significantly affects the efficiency and outcome of the reduction.
-
Optimal Temperature Range: The reduction temperature for MnO₂ to MnO using carbon typically ranges from 700°C to 1000°C. If the temperature is too low, the reduction process will be slow and inefficient, leading to incomplete reduction and lower yields of MnO. Conversely, temperatures that are too high could result in the over-reduction of MnO to metallic manganese, which may not be desirable depending on the application.
-
Effect on Reaction Rate and Yield: At higher temperatures, the carbon can more effectively reduce manganese dioxide, leading to a higher yield of manganese oxide. However, excessive temperatures can also result in the formation of byproducts or cause the degradation of the furnace lining. Therefore, controlling the reduction temperature is key to achieving the desired outcome in the manganese extraction process.
-
Industrial Relevance: In industrial settings, maintaining a consistent and precise reduction temperature is essential for optimizing energy consumption, ensuring product quality, and improving process efficiency. Therefore, controlling the temperature within the optimal range is a critical step in ensuring the successful production of manganese oxide.
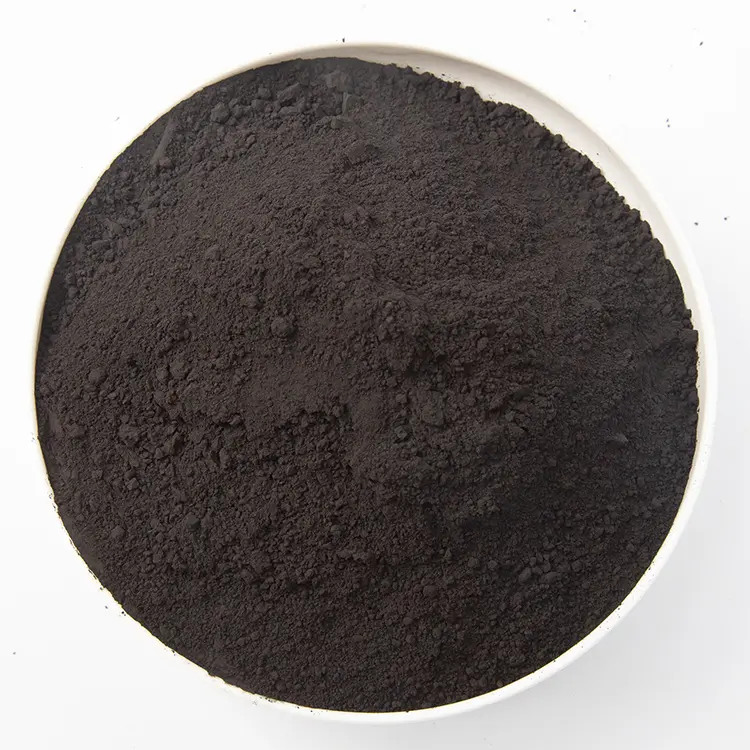
4. Applications of Manganese Oxide (MnO)
Manganese oxide, produced through the reduction of manganese dioxide, has a broad range of applications in various industries:
- Steel Production: Manganese oxide plays a crucial role in steelmaking, where it is used as a deoxidizer. It helps to remove excess oxygen from molten steel, improving the quality and strength of the final product.
- Battery Manufacturing: Manganese oxide is also an essential component in battery manufacturing, especially for lithium-ion batteries. The compound’s high electrochemical stability makes it ideal for use in cathodes, contributing to better performance and longer battery life.
- Catalysis: Manganese oxide is used as a catalyst in various chemical reactions, particularly in the synthesis of organic compounds and in environmental applications such as catalytic converters.
- Water Treatment: MnO is used in water purification processes to remove contaminants such as iron and hydrogen sulfide from drinking water.
5. Industrial Considerations in the Reduction Process
The process of reducing manganese dioxide to manganese oxide using carbon involves careful control of several variables to ensure efficiency:
-
Carbon Quality: The type of carbon used in the reduction process plays a significant role in determining the reaction’s efficiency. High-quality carbon sources, such as petroleum coke or graphite, are preferred for achieving a higher reduction rate.
-
Furnace Design: The design of the furnace or reactor used for the reduction reaction is also crucial. Modern furnaces are designed to maintain temperature consistency and maximize the efficiency of the reduction process.
-
Environmental Considerations: The release of CO₂ as a byproduct of the reduction reaction requires consideration of environmental impact. Many industries are exploring ways to capture and mitigate CO₂ emissions, making the process more sustainable.
Conclusion
The reduction of manganese dioxide to manganese oxide using carbon is a vital process in various industries, particularly in the production of high-purity manganese for steelmaking, battery production, and water treatment. The key to success in this process lies in maintaining the proper reduction temperature, optimizing carbon quality, and controlling other variables that impact the reaction.
By understanding the intricate relationship between MnO₂ and MnO and the factors that influence their reduction, industries can ensure the efficient and sustainable production of manganese oxide for a wide range of applications.
Learn more from BTLnewmaterial
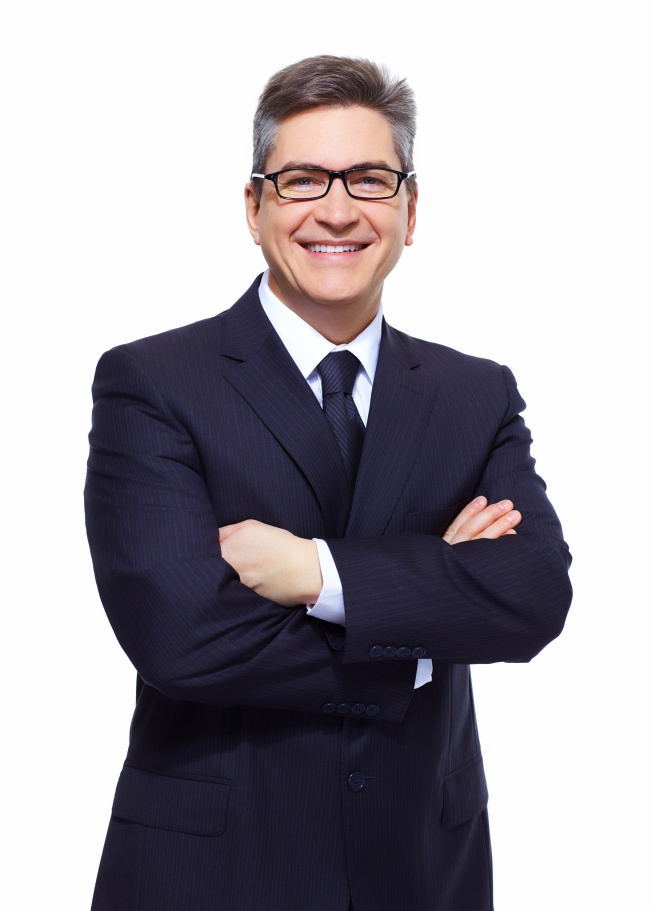
I am Edward lee, CEO of BTLnewmaterial, an engineer and international sales with more than 10 years experience
reach me to discuss more custom solutions for your business.