Manganese carbonate (MnCO₃) is a crucial component in various industries, including battery manufacturing, ceramics, and agriculture. As a business looking to procure manganese carbonate, selecting the right supplier is critical to ensuring the quality of your final products. In this blog, we will guide you through how to evaluate potential suppliers, focusing on key factors like product quality, standards, and production processes.
Keytakeaways: how to find mangaese carbonate supplier
Manganese carbonate, with the chemical formula MnCO₃, is a white to pale pinkish compound used in a variety of industrial applications. It is primarily utilized in the production of dry-cell batteries, as a pigment in ceramics and glass, and as a source of manganese in fertilizers.
Before diving into the supplier selection process, it’s important to understand the basic features of manganese carbonate:
- Chemical Formula: MnCO₃
- Physical Properties: Manganese carbonate is typically found as a powder or crystalline solid. It has low solubility in water and is stable under normal conditions.
2. Determining the Quality Standards
Quality is the most critical factor when selecting a manganese carbonate supplier. Here’s how to determine the quality of the manganese carbonate offered:
a. Purity Levels
The purity of manganese carbonate is one of the most important indicators of quality. Manganese carbonate is typically available in various purity levels, such as:
- High-Purity MnCO₃: With a purity of 98% or higher, high-purity manganese carbonate is ideal for applications in battery manufacturing and high-performance chemical processes.
- Industrial-Grade MnCO₃: With a purity of around 90-95%, this grade is used in less sensitive applications, such as in the production of ceramics or as a pigment.
Purity impacts the performance of your final products. For example, in battery manufacturing, higher purity manganese carbonate results in better battery efficiency and longevity.
b. Impurity Control
In addition to purity, it’s essential to consider the levels of impurities in the manganese carbonate. Common impurities include:
- Iron (Fe): High iron content can compromise the effectiveness of manganese carbonate in some applications, particularly in batteries and electronics.
- Sulfur (S): High sulfur content can reduce the quality of manganese carbonate used in certain chemical processes.
A good supplier will provide detailed analysis reports showing the concentration of impurities and ensuring they meet industry standards.
c. Granulation and Particle Size
Manganese carbonate is available in different granulations (fine powder or granular form). Depending on your application, the particle size may significantly impact the material’s performance.
- Fine Powder: Best for battery production, where uniformity and consistency are essential.
- Coarse Granules: Typically used in ceramics and glass manufacturing.
Suppliers should be able to offer tailored granulation and particle size distribution to meet your specific needs.
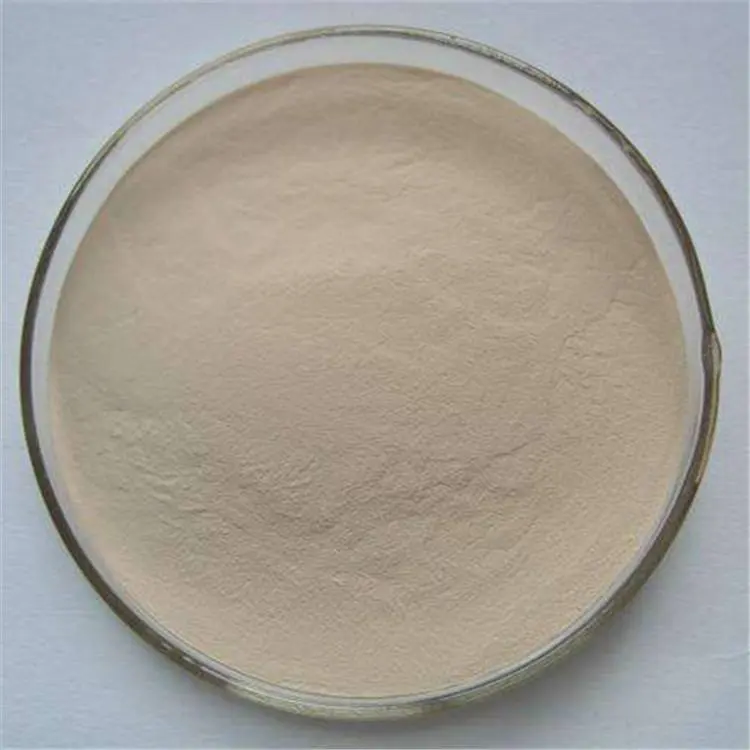
3. Production Process and Technology
The manufacturing process of manganese carbonate directly affects its quality. When evaluating suppliers, you should ask about their production methods and technology:
a. Synthesis Process
Manganese carbonate is usually produced via one of the following processes:
-
Precipitation Method: This involves reacting a manganese salt, typically manganese sulfate (MnSO₄), with sodium carbonate (Na₂CO₃). The result is manganese carbonate precipitate, which is then filtered, washed, and dried.
-
Direct Extraction from Manganese Ore: In this method, manganese oxide ore is treated with carbon dioxide to form manganese carbonate. This method is generally used for lower purity grades.
Both processes have their advantages, but the precipitation method is typically preferred for producing high-purity manganese carbonate.
b. Quality Control and Consistency
A good supplier will have stringent quality control measures in place throughout the production process. This includes checking:
- Raw Material Quality: Ensuring that the source manganese ore or salts are free from impurities.
- Production Parameters: Maintaining optimal temperature, pressure, and chemical ratios during the synthesis process.
- Post-Production Testing: Running batch tests to verify the consistency and purity of the final product.
Look for suppliers who can provide production batch records and offer traceability in case of quality issues.
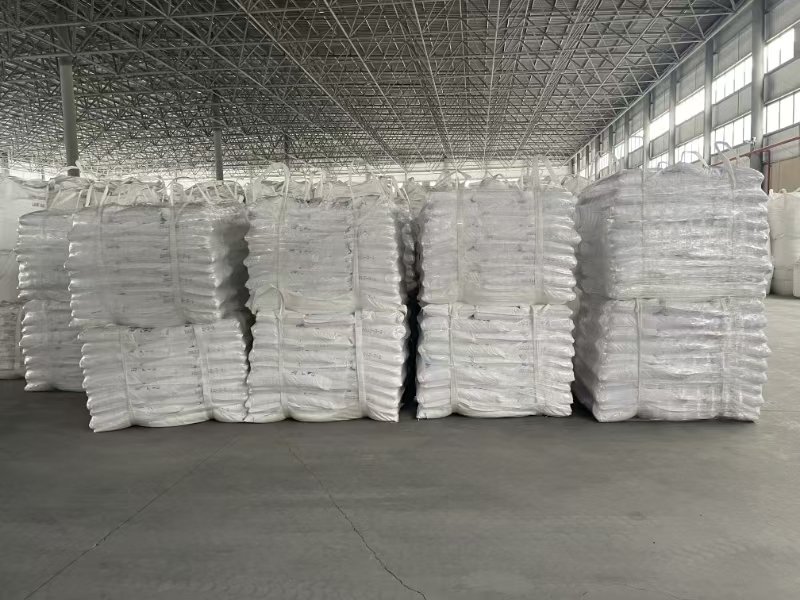
4. Effects of Different Purity Standards
The purity of manganese carbonate has a direct impact on its application:
-
High Purity (98% and above):
- Applications: Primarily used in industries requiring high performance, such as lithium-ion batteries, catalyst production, and high-end electronics.
- Benefits: Increased efficiency, longer life cycles, and fewer impurities leading to higher-end product performance.
-
Standard Purity (90-95%):
- Applications: Suitable for non-critical applications like pigments, agricultural fertilizers, and low-end industrial chemicals.
- Benefits: Cost-effective and sufficient for industries where impurities do not significantly affect the final product.
Selecting the right grade based on your industry is crucial for optimizing performance and minimizing costs.
5. Evaluating Supplier Capabilities
While quality is important, the reliability of the supplier is just as crucial. Here’s what to consider when evaluating potential manganese carbonate suppliers:
a. Manufacturing Capacity
Ensure that the supplier can meet your volume requirements, whether you’re buying in bulk or need a smaller, custom order. Ask about their monthly production capacity and whether they can handle increased demand if needed.
b. Lead Time and Delivery
Choose a supplier who can guarantee timely delivery. Delays in raw material supply can significantly impact your production schedule. Look for suppliers who offer flexibility in shipping methods, such as international freight services if you are sourcing globally.
c. Customer Service and Support
A reliable supplier will offer excellent customer support, including after-sales service. This could include technical assistance, quality issue resolution, and product guarantees.
Conclusion
Choosing the right manganese carbonate supplier requires careful evaluation of factors like purity, impurity levels, production methods, and supplier reliability. By focusing on these aspects, you can ensure that you are selecting a high-quality product that meets your needs.
To summarize:
- Purity and Impurity Control: Ensure the manganese carbonate has the appropriate purity for your application and that impurities are kept to a minimum.
- Production Process: Choose suppliers with proven, high-quality manufacturing processes.
- Supplier Reliability: Ensure your supplier can meet your volume, delivery, and customer service expectations.
If you’re looking for a reliable supplier of high-quality manganese carbonate, feel free to contact us. We offer premium manganese carbonate with a focus on purity, consistency, and timely delivery.
We are global supplier of manganese dioxide,manganese carbonate and manganese sand filter.
Contact me to provide custom solutions to boost your business.
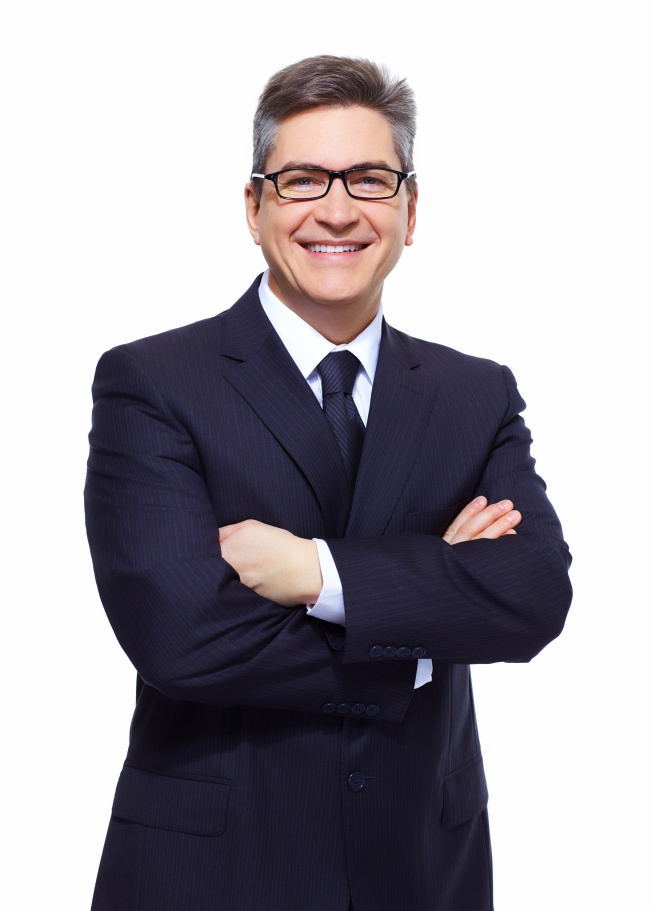
I am Edward lee, CEO of BTLnewmaterial, an engineer and international sales with more than 10 years experience
reach me to discuss more custom solutions for your business.