Activated manganese dioxide is a vital industrial chemical widely recognized for its excellent catalytic properties and efficiency in various applications. Whether you are involved in battery manufacturing, chemical synthesis, or environmental remediation, ensuring the correct use, storage, and transportation of activated manganese dioxide is crucial for achieving optimal performance and maintaining safety standards. This guide serves as an in-depth manual for customers, offering detailed operating procedures, best practices, and answers to frequently asked questions (FAQ) to help you maximize the benefits of this key material.
In this blog, we will cover:
- An overview of activated manganese dioxide
- Detailed usage guidelines
- Storage recommendations
- Transportation protocols
- Safety precautions and best practices
- A comprehensive FAQ section
- Additional tips and customer support resources
By following the recommendations provided in this guide, you can ensure that your handling of activated manganese dioxide remains both safe and efficient throughout its lifecycle—from receipt and storage to usage and disposal.
Activated manganese dioxide is a specially processed form of manganese dioxide that has been treated to enhance its physical and chemical properties. This activated variant is characterized by its higher surface area and improved catalytic activity, making it ideal for applications where efficiency is paramount.
1.1 What Is Activated Manganese Dioxide?
Activated manganese dioxide is produced through a process that “activates” the raw material by increasing its porosity and reactivity. Unlike its natural or unmodified counterpart, the activated form provides superior performance in catalytic reactions, oxidation processes, and electrochemical applications. Its high surface area facilitates enhanced interaction with reactants, leading to faster and more efficient reactions.
1.2 Key Applications
Some of the most common applications include:
- Battery Manufacturing: Used in alkaline batteries to improve performance and longevity.
- Catalysis: Acts as an oxidizing agent in various chemical reactions.
- Environmental Remediation: Helps in treating industrial wastewater and reducing harmful emissions.
- Chemical Synthesis: Employed as a catalyst in organic and inorganic chemical processes.
For further reading on manganese dioxide and its applications, consider visiting the Wikipedia page on Manganese Dioxide.
1.3 Why Proper Handling Matters
The unique properties of activated manganese dioxide require specialized handling procedures. Improper use, storage, or transportation can not only reduce its effectiveness but may also pose safety risks to personnel and equipment. By adhering to the guidelines in this manual, customers can ensure that the product maintains its high quality and performs reliably in all intended applications.
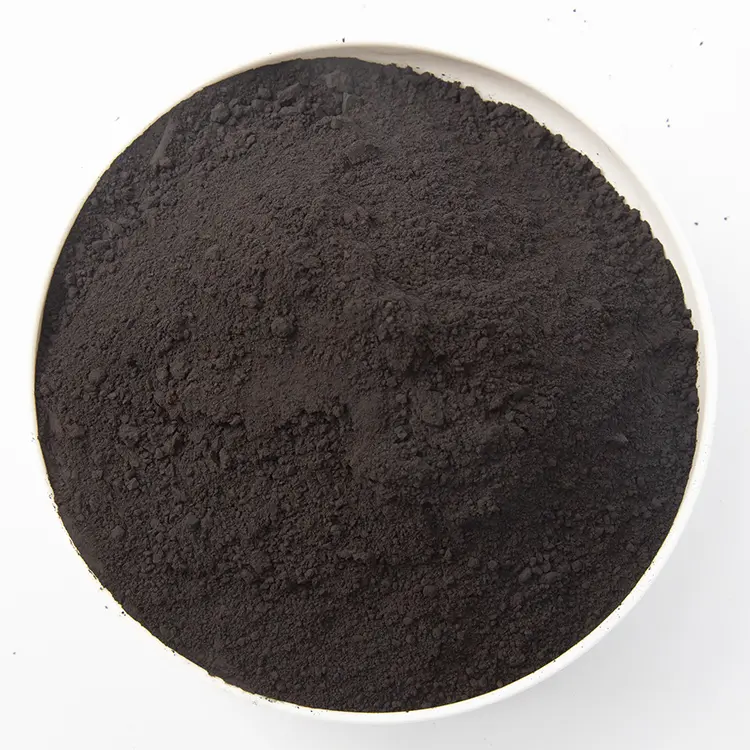
2. Detailed Usage Guidelines
Correct usage of activated manganese dioxide is critical to achieving the desired outcomes in your industrial processes. This section provides step-by-step instructions, practical tips, and best practices to ensure that you handle the material correctly.
2.1 Handling Procedures
- Personal Protective Equipment (PPE): Always wear appropriate PPE, including gloves, safety goggles, and lab coats. For more detailed safety information, refer to the OSHA guidelines on chemical handling.
- Ventilation: Ensure that the area where activated manganese dioxide is used is well-ventilated to avoid inhalation of fine particles.
- Minimize Dust Generation: Use gentle handling techniques to minimize dust. Employ dust collection systems if available.
- Spill Response: In case of a spill, follow your facility’s hazardous material cleanup procedures immediately. Keep a spill kit readily available, and consult your local environmental safety guidelines.
2.2 Mixing and Application
- Dosage Recommendations: Follow your process specifications or the supplier’s recommendations on dosage. Incorrect dosing can lead to inefficient reactions or safety hazards.
- Mixing Instructions:
- Dry Mixing: For some applications, activated manganese dioxide may be mixed in its dry form. Ensure even distribution by using industrial mixers that provide consistent blending.
- Wet Mixing: When preparing a slurry, gradually add the activated manganese dioxide to the liquid medium while stirring continuously to prevent clumping.
- Temperature Considerations: Certain applications require controlled temperatures to maintain reactivity. Monitor and adjust the temperature according to process requirements.
- Compatibility Checks: Always verify that the activated manganese dioxide is chemically compatible with other substances in your process to avoid unwanted reactions.
2.3 Application Techniques
- Catalytic Reactions: Utilize the high surface area of activated manganese dioxide by ensuring it is evenly dispersed in the reaction mixture. Its catalytic properties are best exploited when the contact between reactants and the catalyst is maximized.
- Electrochemical Applications: In battery production, ensure that the activated manganese dioxide is uniformly layered to improve conductivity and overall battery performance.
- Environmental Applications: When used for water treatment, the material should be mixed thoroughly with the wastewater to ensure optimal contaminant breakdown.
2.4 Troubleshooting Common Usage Issues
- Reduced Reactivity: If the performance of activated manganese dioxide appears diminished, check for potential causes such as contamination, moisture absorption, or degradation due to improper storage.
- Clumping or Caking: This may indicate that the material has been exposed to moisture. If clumping occurs, carefully break up the material using a clean, dry tool.
- Inefficient Mixing: Poor mixing can lead to uneven distribution of the material. Utilize mechanical mixers to achieve a consistent blend, especially for large batches.
By following these detailed usage guidelines, customers can optimize the performance of activated manganese dioxide in their respective applications and ensure that the product’s exceptional properties are fully utilized.
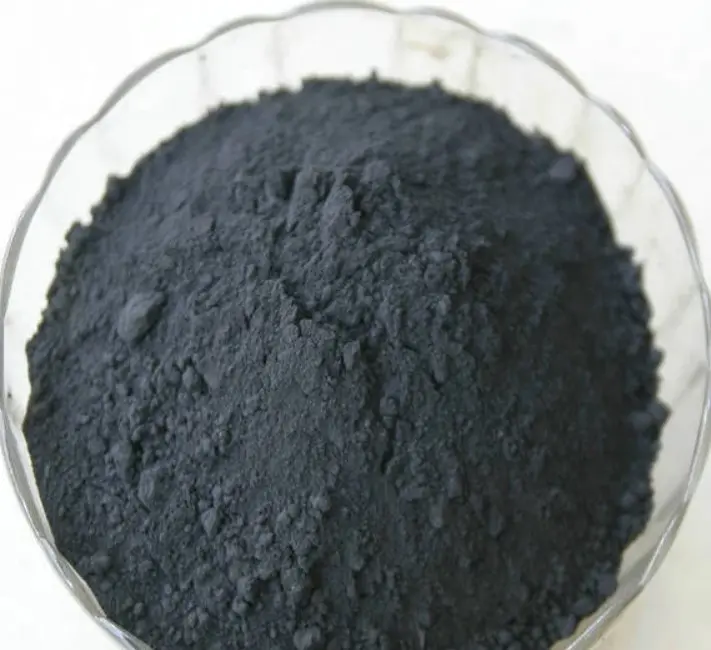
3. Storage Guidelines
Proper storage of activated manganese dioxide is essential to maintain its quality and performance over time. This section outlines best practices for storing the material safely and effectively.
3.1 Ideal Storage Conditions
- Temperature Control: Store activated manganese dioxide in a cool, dry place. High temperatures can compromise its properties, so maintaining a stable, moderate temperature is essential.
- Humidity: Keep the storage area free of moisture. Activated manganese dioxide is hygroscopic, meaning it can absorb moisture from the air, which may lead to clumping or chemical degradation.
- Ventilation: Ensure the storage area is well-ventilated to prevent the buildup of dust and potential contaminants.
3.2 Container Selection
- Sealed Containers: Use airtight, non-reactive containers to prevent exposure to humidity and contaminants. Containers made of high-density polyethylene (HDPE) or stainless steel are recommended.
- Labeling: Clearly label containers with the product name, batch number, and storage date. This helps in maintaining inventory control and tracking product shelf-life.
- Secondary Containment: Consider using secondary containment measures (such as spill pallets or containment bins) to protect against accidental leaks or spills.
3.3 Handling During Storage
- Regular Inspections: Periodically inspect storage containers for signs of moisture, damage, or contamination. Early detection of issues can prevent further degradation of the product.
- Segregation of Chemicals: Avoid storing activated manganese dioxide with incompatible chemicals. Consult the EPA guidelines for chemical storage best practices to ensure that your storage setup complies with safety standards.
- Rotation of Stock: Implement a first-in, first-out (FIFO) system to ensure that older inventory is used before newer batches. This practice helps maintain product quality and reduces the risk of degradation.
3.4 Long-Term Storage Considerations
- Shelf Life: Monitor the shelf life of activated manganese dioxide. Even when stored under ideal conditions, chemical properties can change over time. Regularly test the material to ensure it still meets the required performance standards.
- Environmental Monitoring: Use environmental monitoring equipment to track temperature and humidity in the storage area. Data loggers can be useful for maintaining records and ensuring that storage conditions remain within the specified range.
- Documentation: Keep detailed records of storage conditions, inspection dates, and any incidents of contamination or degradation. This documentation is invaluable for quality control and regulatory compliance.
Following these storage guidelines will help you preserve the quality and effectiveness of activated manganese dioxide, ensuring that it remains in optimal condition until it is ready for use.
4. Transportation Guidelines
Transporting activated manganese dioxide safely is as critical as proper usage and storage. This section outlines the best practices for packaging, labeling, and shipping the material to prevent damage and ensure compliance with transportation regulations.
4.1 Packaging Requirements
- Primary Packaging: Use robust, non-reactive primary packaging materials. Containers should be resistant to moisture and physical damage. HDPE drums or sealed bags are commonly used.
- Secondary Packaging: For added protection, place the primary packaging within a secondary containment system, such as a cardboard box or wooden crate, to absorb shocks during transit.
- Padding and Cushioning: Use appropriate cushioning materials (e.g., foam or bubble wrap) to prevent movement within the container during transportation.
4.2 Labeling and Documentation
- Hazard Labels: Clearly mark all containers with the appropriate hazard symbols and labels in accordance with the Globally Harmonized System (GHS) of classification and labeling of chemicals.
- Shipping Documentation: Include detailed documentation such as Material Safety Data Sheets (MSDS), certificates of analysis, and transportation permits if required by local or international regulations.
- Contact Information: Ensure that shipping labels include emergency contact details for both the supplier and the receiving facility.
4.3 Transportation Best Practices
- Mode of Transportation: Choose a transportation method that minimizes the risk of exposure to extreme conditions. For example, temperature-controlled vehicles may be necessary for long-distance shipping.
- Compliance with Regulations: Verify that your transportation methods comply with relevant national and international regulations regarding the shipment of hazardous materials. Check the International Air Transport Association (IATA) guidelines for air shipments and local transportation authorities for ground shipments.
- Handling Procedures: Train all personnel involved in the transportation process on proper handling techniques and emergency response procedures. This includes loading, unloading, and securing the material during transit.
- Monitoring During Transit: Use tracking systems and environmental sensors to monitor conditions during transport. This data can help ensure that the product remains within acceptable temperature and humidity ranges throughout its journey.
4.4 Emergency Procedures During Transportation
- Spill Response: In the event of a spill during transportation, drivers and handlers should immediately secure the area, notify emergency services, and follow the spill response protocols outlined in the MSDS.
- Communication Protocols: Establish clear communication protocols between transporters, the supplier, and the receiving facility to address any issues that arise during transit quickly.
- Incident Reporting: Document any incidents during transportation for continuous improvement of your shipping procedures and to comply with regulatory requirements.
Adhering to these transportation guidelines will help ensure that activated manganese dioxide arrives at its destination safely and in optimal condition for immediate use.
5. Safety Precautions and Best Practices
The handling of activated manganese dioxide requires strict adherence to safety protocols. This section outlines the best practices for maintaining a safe working environment when using, storing, and transporting this material.
5.1 Personal Protective Equipment (PPE)
- Mandatory PPE: Always wear gloves, safety goggles, and protective clothing when handling activated manganese dioxide. A respirator may be necessary in environments with high dust levels.
- PPE Maintenance: Regularly inspect and maintain PPE to ensure it remains effective. Replace any damaged or worn-out equipment immediately.
5.2 Workplace Safety Measures
- Ventilation Systems: Install and maintain proper ventilation systems in areas where activated manganese dioxide is used to reduce airborne particulate matter.
- Signage and Labeling: Post clear signage in work areas to warn of potential hazards. Ensure that all containers and storage areas are labeled with safety instructions.
- Training and Education: Regularly train employees on the hazards of activated manganese dioxide and the correct procedures for handling, storage, and transportation. Consider enrolling your team in specialized courses offered by organizations like the American Chemical Society (ACS).
5.3 Emergency Preparedness
- Emergency Plans: Develop and practice emergency response plans for incidents such as spills, fires, or accidental exposure. Ensure all personnel are familiar with evacuation routes and emergency contact information.
- First Aid Measures: Maintain well-stocked first aid kits in areas where the material is handled. Provide training on first aid measures specifically related to chemical exposures.
- Incident Reporting: Implement a robust system for reporting and analyzing safety incidents to prevent recurrence and continuously improve workplace safety.
5.4 Environmental Considerations
- Waste Disposal: Dispose of waste containing activated manganese dioxide in accordance with local environmental regulations. Consult your local environmental agency or the EPA for guidance on proper disposal methods.
- Spill Containment: Equip your facility with spill containment materials and follow recommended cleanup procedures immediately after any incident.
- Sustainable Practices: Explore options for recycling or reusing activated manganese dioxide where possible, and consider working with suppliers who prioritize sustainable production practices.
By implementing these safety precautions and best practices, you can minimize risks and ensure that the use of activated manganese dioxide contributes to a safe and productive work environment.
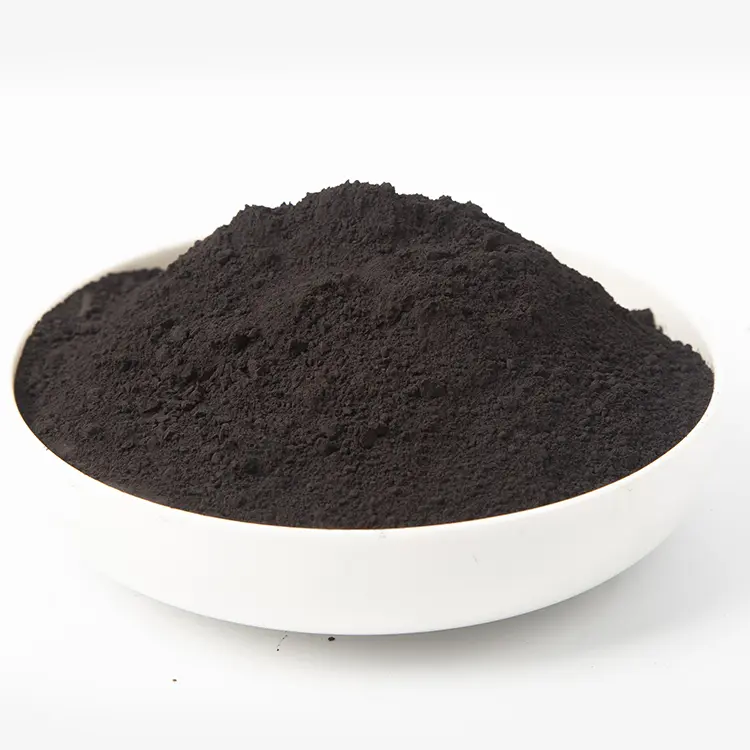
6. Frequently Asked Questions (FAQ)
This FAQ section addresses common questions and concerns related to the handling and use of activated manganese dioxide. If you have additional queries, please consult your supplier or reach out to our customer support team.
Q1: What is activated manganese dioxide, and how does it differ from regular manganese dioxide?
A: Activated manganese dioxide is a modified form of manganese dioxide that has been treated to increase its surface area and catalytic activity. This activation process enhances its performance in various industrial applications, particularly in catalysis and battery production, compared to unmodified manganese dioxide.
Q2: What are the primary applications of activated manganese dioxide?
A: Activated manganese dioxide is used in battery manufacturing, catalysis, environmental remediation, and chemical synthesis. Its high reactivity makes it particularly effective in processes requiring oxidation or enhanced catalytic activity.
Q3: How should I handle activated manganese dioxide safely?
A: Always wear appropriate PPE (gloves, goggles, and protective clothing), work in well-ventilated areas, and follow your facility’s safety protocols. Refer to OSHA guidelines for more detailed information on safe handling practices.
Q4: What are the ideal storage conditions for activated manganese dioxide?
A: Store the material in a cool, dry, and well-ventilated area, using sealed, non-reactive containers to protect it from moisture and contaminants. Regularly inspect storage conditions and implement a FIFO (first-in, first-out) system to ensure product freshness.
Q5: What precautions should I take during transportation?
A: Use robust, sealed packaging, clearly label containers with hazard symbols, and ensure that all documentation (including MSDS) accompanies the shipment. Follow national and international guidelines for transporting hazardous materials.
Q6: How can I prevent clumping or degradation of activated manganese dioxide?
A: Ensure that the product is stored in a moisture-free environment and handled gently to avoid creating dust. If clumping occurs, break up the material carefully using a clean, dry tool.
Q7: What steps should be taken if there is a spill?
A: Immediately secure the area, notify emergency responders, and follow your facility’s spill response protocols. Use appropriate spill kits and personal protective equipment to manage the incident safely.
Q8: Is activated manganese dioxide compatible with other chemicals in my process?
A: Always perform a compatibility test when introducing activated manganese dioxide into a new process. Consult your supplier’s technical data sheet and conduct small-scale trials before full-scale application.
Q9: How long is the shelf life of activated manganese dioxide?
A: The shelf life can vary depending on storage conditions. Under ideal conditions, the product maintains its properties for an extended period, but regular quality testing is recommended to ensure performance standards are met.
Q10: Who can I contact for further technical support or customer service?
A: If you have any further questions or require technical assistance, please contact our customer support team. We are committed to helping you optimize your use of activated manganese dioxide safely and effectively.
7. Additional Tips and Customer Support Resources
Ensuring that you get the best performance from activated manganese dioxide often means staying informed about best practices and emerging industry trends. Here are a few additional tips and resources:
7.1 Regular Training and Updates
- Employee Training: Schedule regular training sessions on proper handling, storage, and emergency response procedures. Keep your team updated on any changes to safety guidelines or industry regulations.
- Industry Conferences and Webinars: Attend industry events and webinars to learn about the latest trends and technological advancements in the field of catalysis and chemical processing.
7.2 Documentation and Record-Keeping
- Maintain Logs: Keep detailed logs of storage conditions, usage rates, and any incidents. This documentation is essential for quality control and regulatory compliance.
- Review Technical Data Sheets: Regularly consult the technical data sheets and safety data sheets provided by your supplier to stay informed about any updates to the product’s handling instructions.
7.3 Contacting Support
- Technical Assistance: Our technical support team is available to help troubleshoot any issues you may encounter with activated manganese dioxide. Whether it’s a question about dosage, compatibility, or emergency procedures, do not hesitate to reach out.
- Feedback and Improvement: We value your feedback. Let us know about any challenges you face or improvements you’d like to see in our handling guidelines. Your input helps us refine our practices and better serve our customers.
For more detailed safety and handling practices, consider reviewing resources provided by reputable organizations such as the American Chemical Society and the EPA.
Conclusion
The proper handling, storage, and transportation of activated manganese dioxide are critical to ensuring its effectiveness and safety in various industrial applications. By following the comprehensive guidelines outlined in this blog, you can optimize the performance of activated manganese dioxide, prevent common issues such as clumping or degradation, and maintain a safe working environment.
Key takeaways include:
- Usage: Adhere strictly to recommended handling procedures, mixing techniques, and dosage guidelines to maximize the catalytic efficiency of activated manganese dioxide.
- Storage: Maintain controlled environmental conditions, use appropriate containers, and practice regular inspections to preserve the material’s integrity.
- Transportation: Use robust packaging and follow regulatory guidelines to ensure that the product arrives safely and in peak condition.
- Safety: Prioritize the use of PPE, implement rigorous training, and develop emergency response plans to mitigate risks associated with chemical handling.
- Support: Utilize the FAQ section and customer support resources to resolve issues promptly and stay updated on best practices.
Implementing these practices will not only improve process efficiency but also contribute to a safer and more productive operational environment. Whether you are scaling up production or refining existing processes, this guide is designed to help you make informed decisions when working with activated manganese dioxide.
For further information and updates on our products and best practices, subscribe to our newsletter or visit our website regularly. We remain committed to supporting our customers with high-quality products and comprehensive technical guidance.
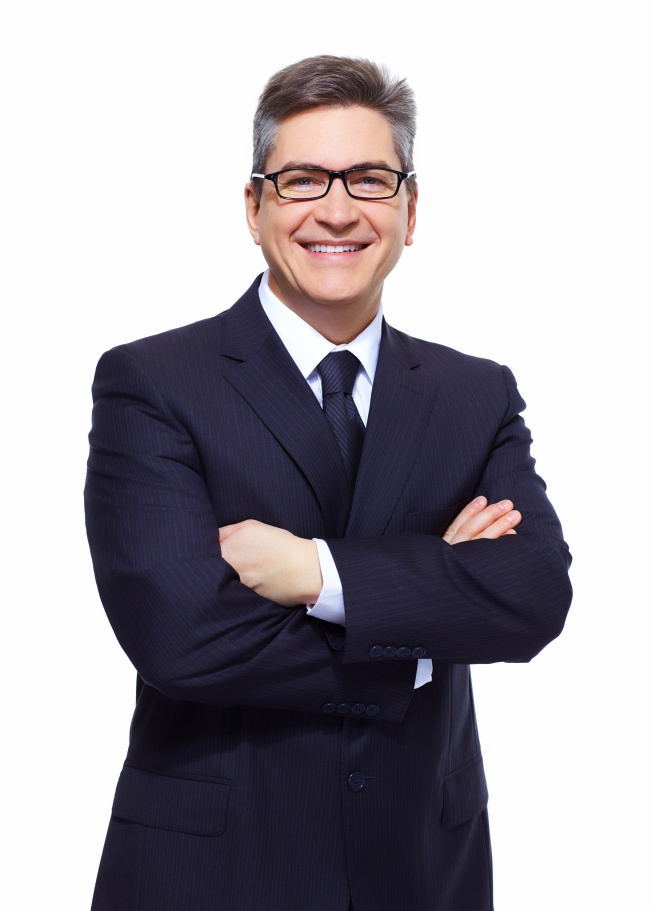
I am Edward lee, CEO of BTLnewmaterial, an engineer and international sales with more than 10 years experience
reach me to discuss more custom solutions for your business.
ogj tgts VTh EGpAm ogKJk