Steel is one of the most widely used materials in construction, manufacturing, and various industrial applications due to its strength, durability, and versatility. However, not all steels are created equal. Manganese steel and carbon steel are two popular types of steel, each with distinct properties that make them suitable for different applications. In this article, we’ll compare manganese steel and carbon steel in terms of their composition, properties, production processes, advantages, disadvantages, and common uses.
Keytakeaways:
What is Manganese Steel?
What is Carbon Steel?
Manganese Steel vs Carbon Steel: A Detailed Comparison
Manganese steel, also known as Hadfield steel, is a high-carbon steel alloy containing 12–14% manganese. It is famous for its toughness, hardness, and resistance to wear and impact. It was first developed by Robert Hadfield in 1882, which is why it’s often referred to as Hadfield steel.
Composition and Properties of Manganese Steel
- Manganese Content: The key characteristic of manganese steel is its high manganese content. Typically, the steel contains 12–14% manganese, which contributes to its remarkable hardness and durability.
- Carbon Content: Manganese steel also contains a higher carbon content (around 0.8–1.25%), which enhances its hardness but can make it less ductile compared to steels with lower carbon content.
- Hardness and Toughness: Manganese steel is highly resistant to wear, shock, and abrasion. This is because the manganese increases the steel’s toughness and improves its resistance to cracking.
- Austenitic Structure: Manganese steel maintains an austenitic microstructure even at room temperature, meaning it can undergo significant deformation without losing strength.
Production Process of Manganese Steel
Manganese steel is produced using a basic oxygen furnace (BOF) or an electric arc furnace (EAF). The production process begins with the addition of high-quality manganese ore to molten iron to increase the manganese content in the steel. The carbon content is controlled during the alloying process by adjusting the carbon inputs. The steel is then cast and treated using heat treatment methods, including quenching and tempering, to achieve the desired hardness and toughness.
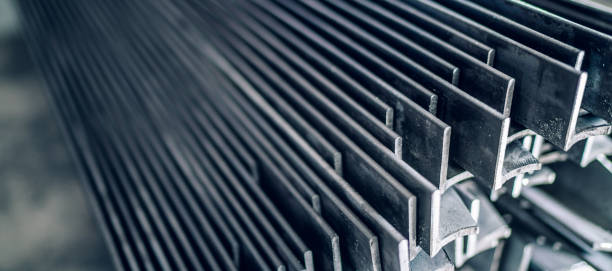
What is Carbon Steel?
Carbon steel, or plain-carbon steel, is one of the most common types of steel used in various applications. It is composed primarily of iron and carbon, with little to no alloying elements. Depending on the amount of carbon present, carbon steel can be classified into three main categories: low-carbon steel, medium-carbon steel, and high-carbon steel.
Composition and Properties of Carbon Steel
- Carbon Content: The carbon content in carbon steel typically ranges from 0.05% to 2.0%. Low-carbon steel contains less than 0.3% carbon, medium-carbon steel contains between 0.3% and 0.6%, and high-carbon steel contains 0.6% to 2.0%.
- Strength and Hardness: Carbon steel’s strength and hardness depend on its carbon content. Higher carbon content increases hardness but reduces ductility and toughness, making the steel more brittle.
- Malleability and Ductility: Carbon steel is malleable and ductile, which means it can be easily shaped, bent, or stretched without breaking, especially when compared to manganese steel. This makes it suitable for various forming processes.
- Weldability: Carbon steel is easier to weld than manganese steel, particularly in the lower-carbon forms. However, higher-carbon steels may require special techniques to avoid cracking during welding.
Production Process of Carbon Steel
Carbon steel is produced by heating iron ore in a blast furnace and adding carbon in the form of coke, a carbon-rich material. The carbon content is adjusted during the process to achieve the desired level of hardness and strength. The steel is then cooled and formed into different shapes and sizes, depending on its intended application. Heat treatment processes like annealing or tempering can be used to adjust the hardness or ductility of the steel.
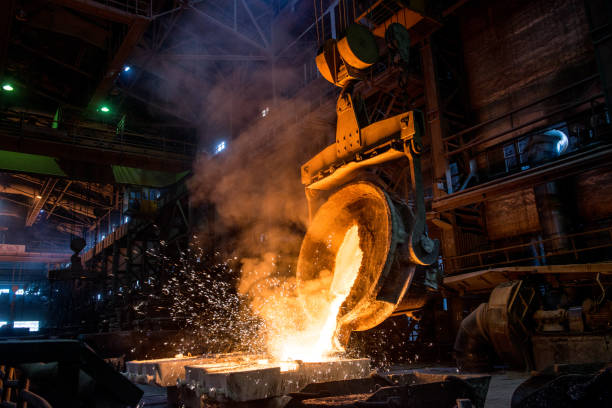
Manganese Steel vs Carbon Steel: A Detailed Comparison
Now that we understand the basics of manganese steel and carbon steel, let’s take a closer look at how they compare in terms of their key properties, advantages, disadvantages, and typical uses.
1. Strength and Hardness
- Manganese Steel: Manganese steel is known for its exceptional strength and hardness. With a high manganese content, this steel can withstand significant wear and tear. Its hardness increases with use, especially when subjected to impact, making it ideal for heavy-duty applications like mining, construction, and railroad tracks.
- Carbon Steel: The strength and hardness of carbon steel depend on its carbon content. While low-carbon steel is not as strong as high-carbon steel, it offers better malleability and ductility. High-carbon steel is stronger but is more brittle and less ductile compared to manganese steel.
2. Toughness and Impact Resistance
- Manganese Steel: One of the key features of manganese steel is its toughness and impact resistance. It can withstand high-impact forces without cracking or breaking, making it ideal for high-stress environments where durability is crucial.
- Carbon Steel: While carbon steel is generally tough, it is not as impact-resistant as manganese steel. The toughness of carbon steel can be improved with heat treatment processes, but it is still not as durable as manganese steel in harsh conditions.
3. Wear and Abrasion Resistance
- Manganese Steel: Manganese steel excels in wear and abrasion resistance. The high manganese content helps the steel form a hardened surface when subjected to wear, making it ideal for applications that involve frequent contact with abrasive materials.
- Carbon Steel: Carbon steel has decent wear resistance, especially in higher-carbon variants. However, it does not match the abrasion resistance of manganese steel, particularly in high-wear applications like mining or aggregate handling.
4. Cost and Availability
- Manganese Steel: Manganese steel is more expensive due to the high manganese content and its specialized applications. Manganese itself is a relatively expensive alloying element, which contributes to the higher cost of manganese steel.
- Carbon Steel: Carbon steel is generally less expensive compared to manganese steel. The cost of production is lower because it primarily consists of iron and carbon, both of which are abundant and less expensive than manganese.
5. Weldability
- Manganese Steel: Manganese steel is more challenging to weld due to its high carbon content and austenitic structure. Specialized welding techniques are required to ensure a strong bond and avoid cracking.
- Carbon Steel: Carbon steel is easier to weld, especially in low-carbon forms. However, welding high-carbon steel may require preheating or post-weld heat treatment to prevent cracking.
6. Corrosion Resistance
- Manganese Steel: Manganese steel does not inherently offer corrosion resistance, but it can be alloyed with other elements to improve its resistance to corrosion. In general, manganese steel is better suited for mechanical strength rather than environmental resistance.
- Carbon Steel: Carbon steel is more susceptible to corrosion than manganese steel, especially in outdoor or wet conditions. It is often coated with protective layers (e.g., galvanizing) to prevent rust and corrosion.
Common Applications: Manganese Steel vs Carbon Steel
Manganese Steel Applications
Due to its toughness, hardness, and resistance to wear and impact, manganese steel is often used in heavy-duty industrial applications, including:
- Mining Equipment: Manganese steel is used for crushers, hoppers, and other mining machinery parts that require high abrasion resistance.
- Railroad Tracks: Manganese steel is often used in the construction of railroad tracks, as it can withstand the heavy impacts from trains without wearing out quickly.
- Construction Equipment: Excavator buckets, bulldozer blades, and other construction equipment often use manganese steel for durability and wear resistance.
- Crusher Parts: Crusher liners, hammers, and other parts in crushing machinery are often made from manganese steel due to its ability to withstand heavy impacts.
Carbon Steel Applications
Carbon steel, due to its variety and lower cost, is used in a wide range of industries. Some common applications include:
- Construction: Carbon steel is used for structural beams, pipes, and reinforcing bars in buildings and infrastructure projects.
- Automotive Industry: Carbon steel is widely used in the manufacturing of automotive parts, such as chassis, body panels, and suspension components.
- Pipes and Tubes: Carbon steel is commonly used to produce pipes and tubes for fluid transportation in industries like oil and gas, water systems, and chemical plants.
- Tools and Machinery: High-carbon steel is used in the production of cutting tools, blades, and other machinery components that require high strength and hardness.
Conclusion: Manganese Steel vs Carbon Steel – Which One Should You Choose?
Both manganese steel and carbon steel have distinct properties that make them suitable for different applications. Manganese steel offers superior toughness, hardness, and wear resistance, making it ideal for heavy-duty, high-impact applications. However, its high cost and challenging weldability can be drawbacks.
On the other hand, carbon steel is more affordable, easier to work with, and versatile, making it the material of choice for a wide range of industries, including construction, automotive, and manufacturing. While carbon steel may not be as resistant to wear and impact as manganese steel, it is still highly durable and can be used effectively in many applications.
Ultimately, the choice between manganese steel and carbon steel depends on the specific needs of your project, including factors such as strength, toughness, cost, and ease of processing. Understanding these key differences will help you make an informed decision and choose the right material for your needs.
FAQ
1. What is the main difference between manganese steel and carbon steel? Manganese steel contains 12–14% manganese, making it highly resistant to wear and impact. Carbon steel, on the other hand, contains mainly iron and carbon and is more affordable and versatile but not as resistant to wear and abrasion as manganese steel.
2. Can manganese steel be welded? Manganese steel can be welded, but it is more challenging due to its high carbon content. Specialized welding techniques are often required to ensure a strong weld.
3. Which steel is more cost-effective, manganese steel or carbon steel? Carbon steel is more cost-effective than manganese steel because it primarily consists of iron and carbon, which are abundant and less expensive than manganese.
4. What are the common uses of manganese steel? Manganese steel is commonly used in heavy-duty applications such as mining equipment, railroad tracks, construction machinery, and crusher parts due to its exceptional toughness and wear resistance.
5. Is carbon steel better for welding? Yes, carbon steel is generally easier to weld than manganese steel, especially in low-carbon forms. High-carbon steel may require special welding techniques to prevent cracking.
We are global supplier of manganese dioxide,manganese carbonate and manganese sand filter.
Contact me to provide custom solutions to boost your business.
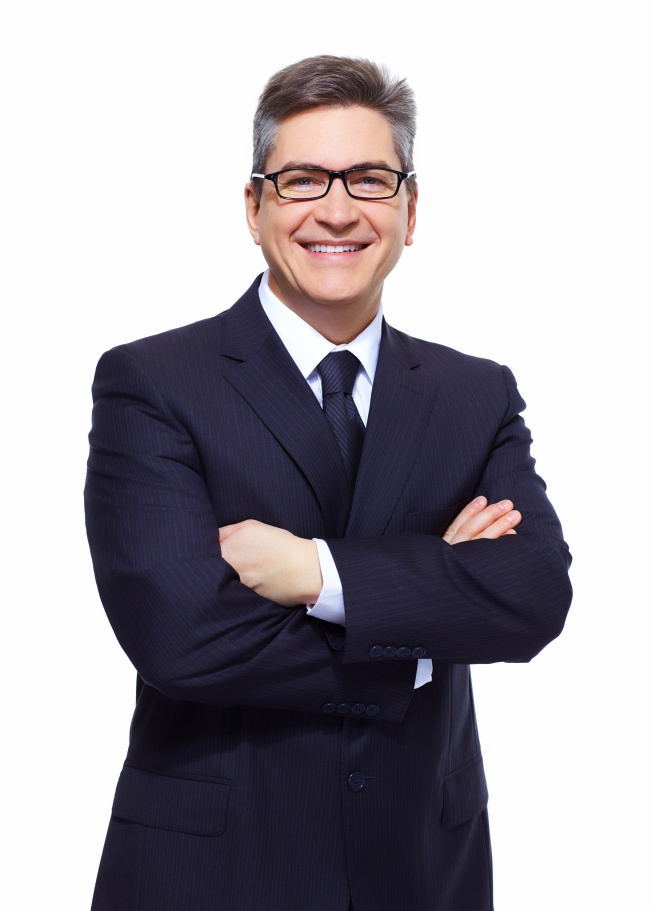
I am Edward lee, CEO of BTLnewmaterial, an engineer and international sales with more than 10 years experience
reach me to discuss more custom solutions for your business.